Cleanliness Analysis of Surfaces
An indispensable part of production
Cleaning processes are an indispensable part of many production and coating processes. They are used to remove unwanted layers, and contaminating films or particles from component surfaces. Cleaning ensures optimal processing of materials such as metal, glass or plastics and polymers. Often, several cleaning approaches are combined to achieve the intended level of cleanliness. It is nevertheless possible that these sophisticated cleaning processes do not lead to the desired success. In those cases residues from production such as oils, greases, polishing agents or abrasives as well as a wide variety of particulate contaminants can remain on the sample surface. This in turn can significantly disrupt further processing steps. At this point, the cleanliness analysis from the Tascon laboratory is often required. In addition to production residues such as particles or contaminant films, the cleaning agents themselves, such as surfactants and additives, can also remain on the surface. The following example shows that residues from a previous cleaning process can nullify the cleaning effect that was aimed for. In the Tascon laboratory the cause of a production problem could be identified and eliminated with the help of a cleanliness analysis.
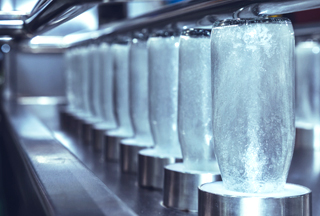
Cleanliness analysis
Surfactant residues as the cause of adhesion problems
Despite complex degreasing and subsequent plasma cleaning, there were adhesion problems on a nickel surface. To clarify this problem, ToF-SIMS was used in our laboratory to carry out a cleanliness analysis and to examine the lateral distribution of the detected substances. The analyses showed that a surfactant based on dodecylbenzene sulphonic acid (DDBS) could be detected on the surface of the cleaned metal. This substance was identified as a component of the cleaning agent that was used. It had not been completely removed from the metal surface due to inadequate rinsing. The subsequent plasma cleaning could not completely remove the DDBS residues, so that the residues triggered an adhesion failure in the next production step. Based on the results of the cleanliness analysis, the final cleaning of the Ni sheets was optimized and the failure rate due to adhesion problems was significantly reduced.
Tascon - Laboratory for cleanliness analysis and residue analysis
In many production processes, cleanliness analysis is a powerful tool to approach issues. In the Tascon laboratory we have decades of experience in the analysis of particulate contaminants using SEM and SEM/EDX as well as in the analysis of contaminating films using the ToF-SIMS technique. If you are interested in our cleanliness analysis, then simply contact Tascon and let us advise you without obligation. Our competent and friendly team is happy to help you. We look forward to your inquiry.
Get in touch. Contact one of our analytical professionals:
(845)-352-1220